With “Old Nick” due to come out of the water next month, to have its “bottom blacked” for the first time, we will soon be able to see the condition of the steel hull and make sure that we have not suffered from any galvanic corrosion.
Generally, steel narrowboats should have their hulls re-painted, referred to as “blacking” due to the black bitumen paint that is used, every 2-3 years. “Old Nick” was launched in December 2020, so it will be just over two years, but with three icy winters (ice is not good for bitumen) we thought it prudent to have it done at the beginning of our third season. Another factor in this decision, was that Droitwich Marina offer a very good and competitive blacking service and so we wanted to get it done before we leave for Brinklow Marina.
Ortomarine, treat all of their hulls with a two part epoxy process, before they black the new hull and “Old Nick” looked fantastic when first launched, I am sure it will not be as clean and shiny now.
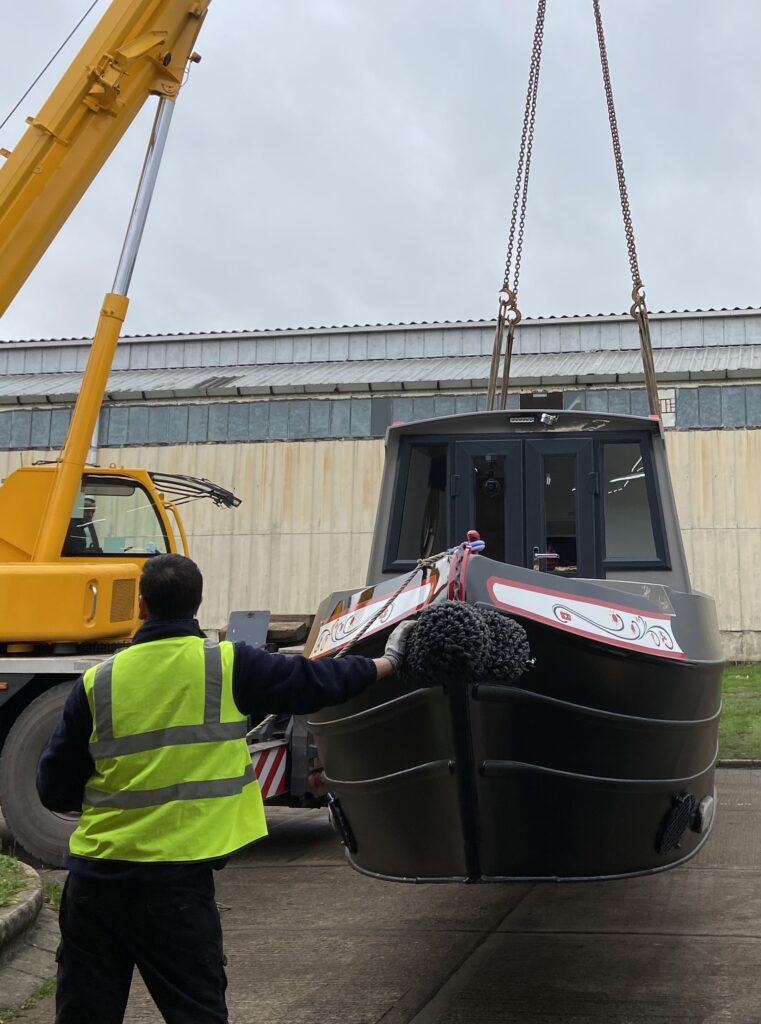
In order for a steel hull to corrode, you need water and oxygen and so even if the hull’s blacking below the waterline is scraped or scratched, it should not suffer natural/uniform corrosion. However, the hull at the waterline will be in constant contact with both water and oxygen and is where most of the corrosion will occur.
There are actually ten different types of corrosion and one of the other types that we should be most wary of on boats, is Galvanic Corrosion. If you studied Chemistry at school, you will almost certainly have watched or taken part in the classic electrolysis experiment, where two electrodes are dropped in to a beaker of copper sulphate and as a DC voltage is applied, you watch one of the electrodes become coated in copper.
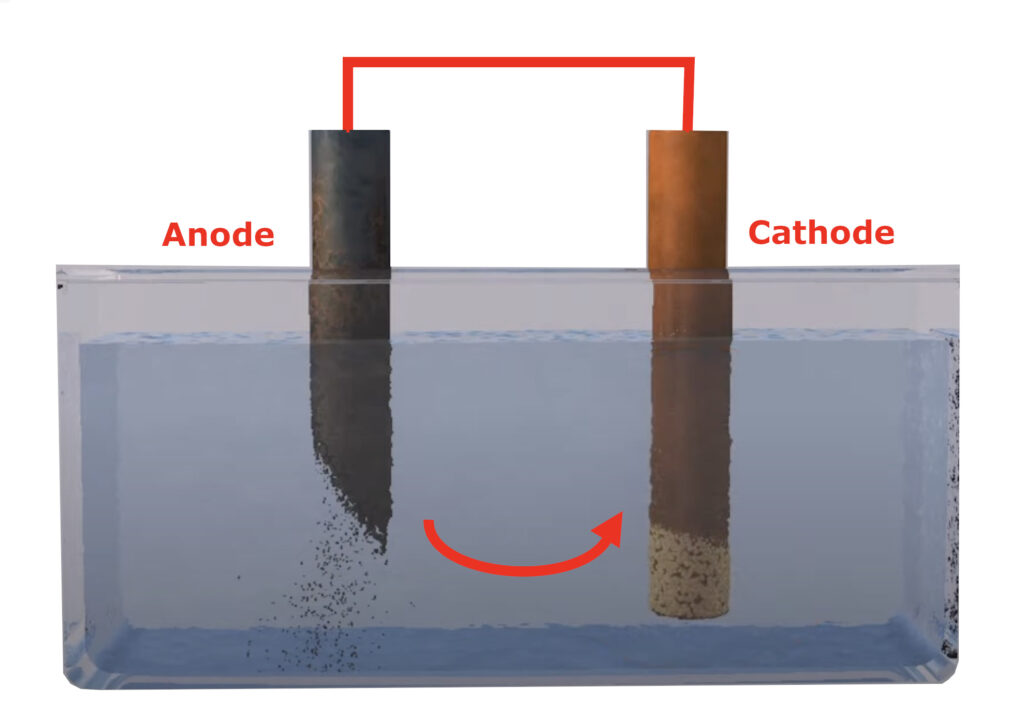
In the same lesson, you were probably told about Nobel metals and how different metals can be more or less prone to corrosion, when immersed in water with another metal. The least nobel metal will start to corrode – lose electrons to the other metal – and if you introduce an external electrical charge to the metals, such as stray currents from other vessels in a marina, the corrosion can increase dramatically.
This is the reason why you should fit Magnesium anodes to your boat’s hull. Magnesium is a less noble metal than steel, so the anodes corrode quicker than the steel, protecting your hull from corrosion. However, if your boat is going to be constantly or regularly moored in a marina on AC mains hook-up, you need additional protection and that is where some form of electrical isolation comes in.
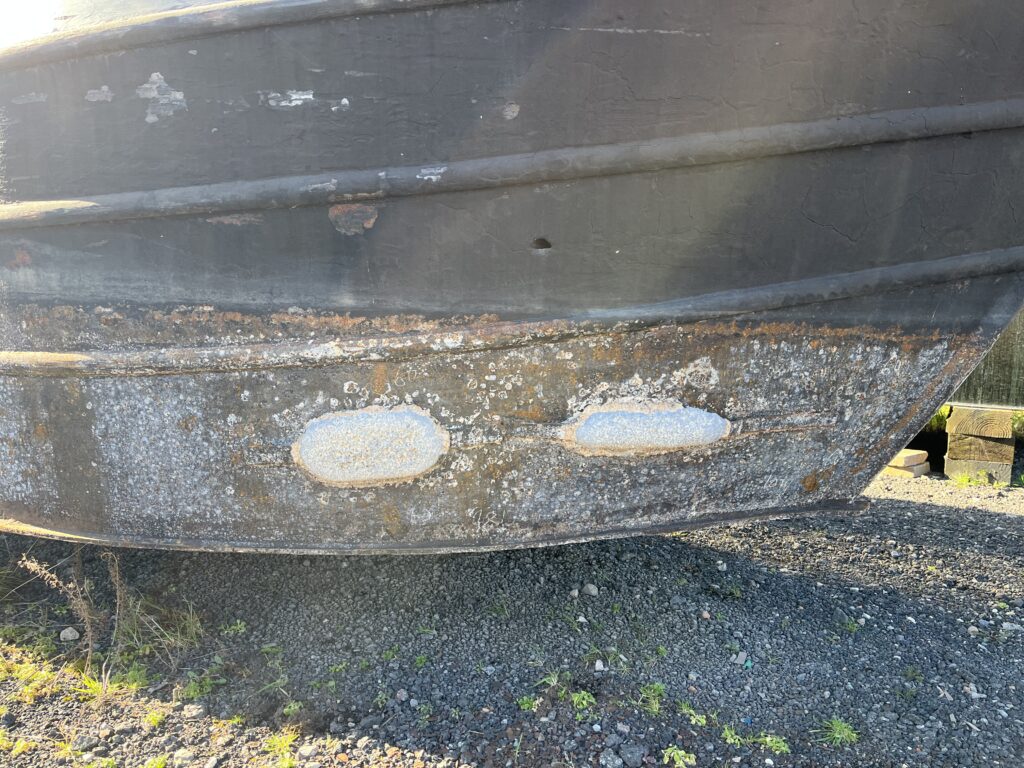
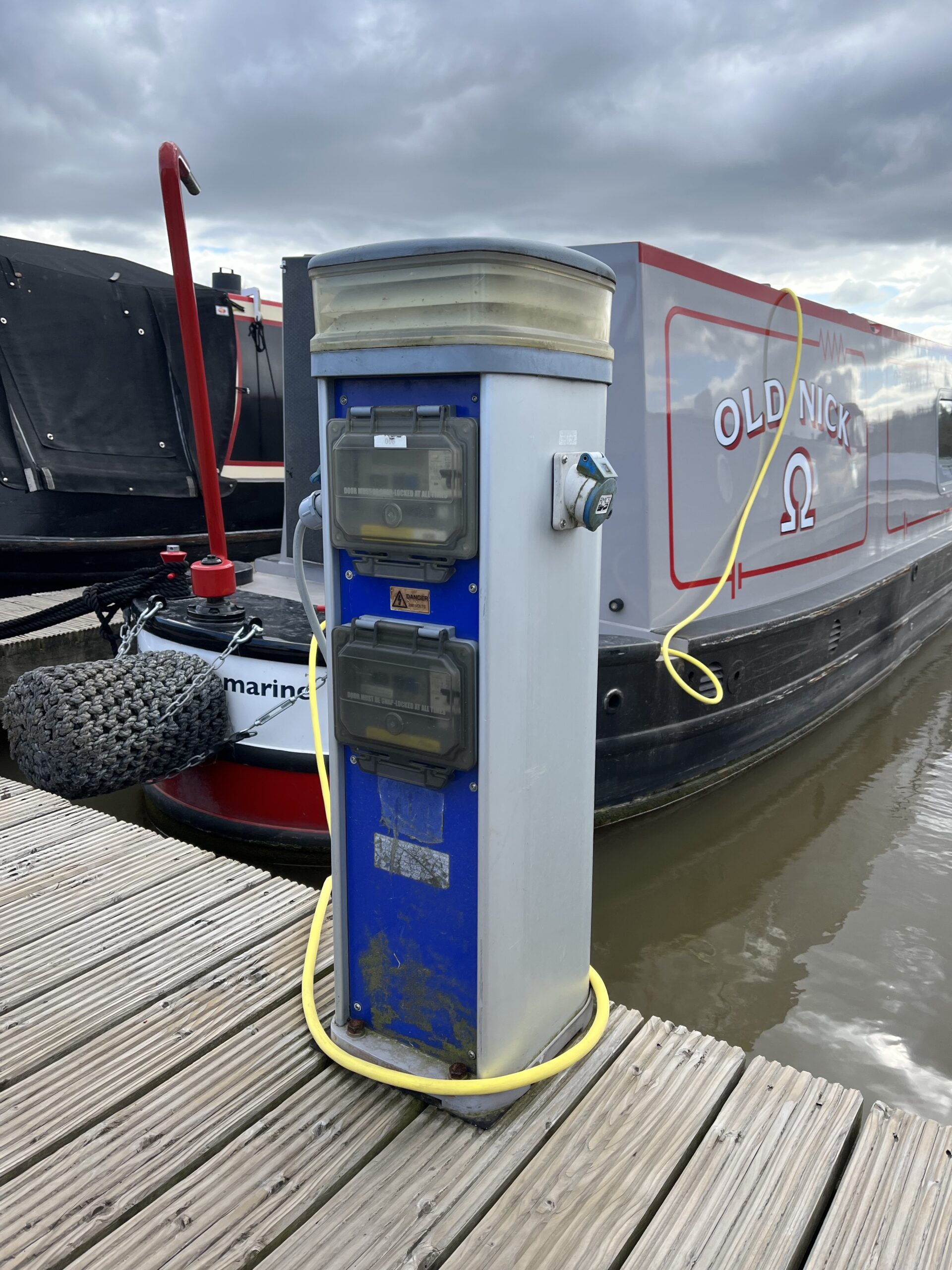
When multiple boats are connected to the AC shore supply in a marina, they all share a common earth connection and just like the electrolysis experiment, any stray currents will accelerate the corrosion process. The only way to stop galvanic corrosion when in a marina, is to electrically isolate your boat from the AC shore supply.
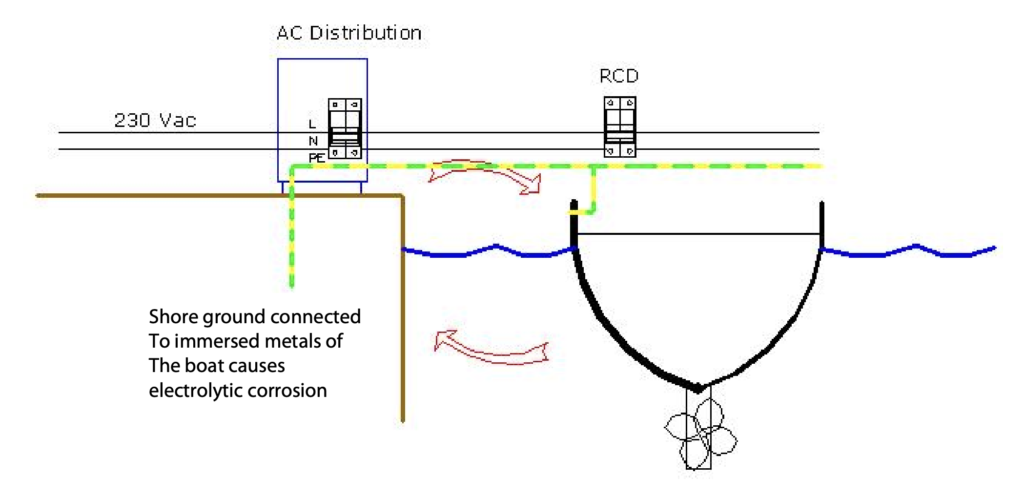
There are two common methods of isolating a boat from the AC shore supply; a Galvanic Isolator (simplest, cheapest and smallest solution) or a full Isolation Transformer.
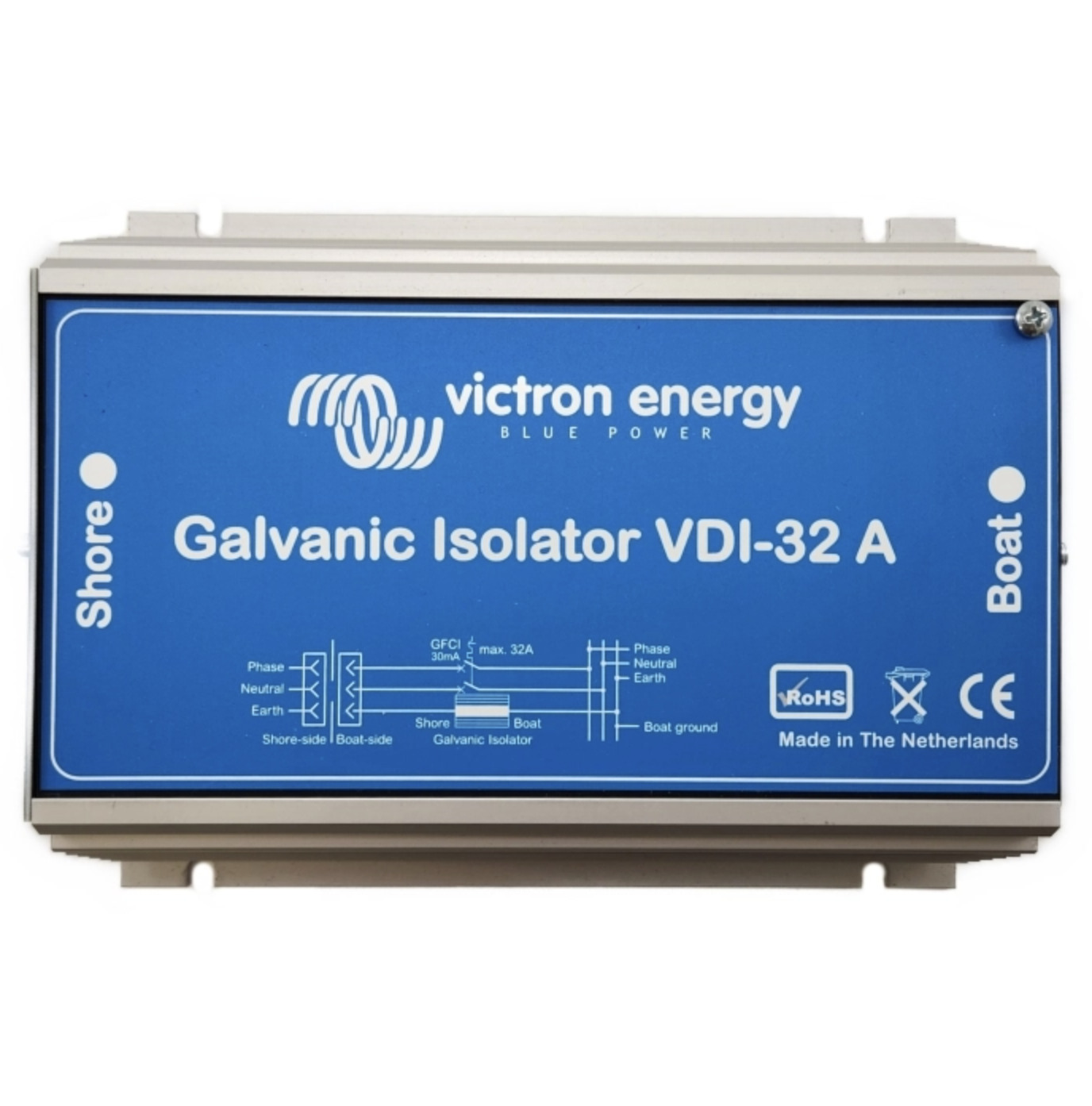
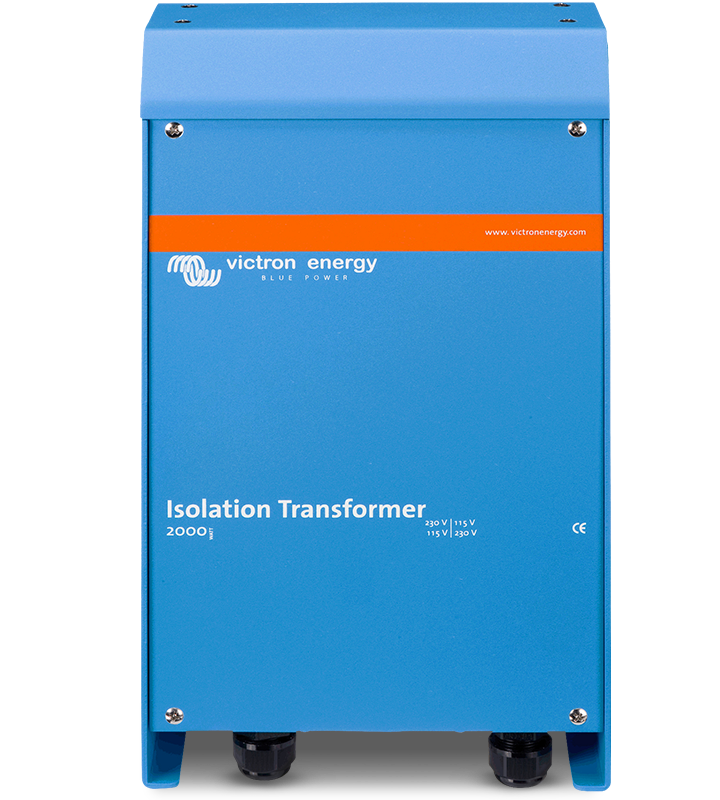
A galvanic isolator sits in the main AC earth wire and blocks the small stray currents that accelerate the galvanic corrosion. A set of diodes inside the galvanic isolator, block small currents from any < 1.4V Voltages that may exist between your hull and other vessels or marina pontoons. NOTE – the current from dangerously large AC voltages, that could electrocute someone are not blocked and so your RCD safety device will continue to protect you.

The galvanic isolator works well in most situations, but if a fault exists in the marina’s AC system or one of the other boats in the marina, that creates a larger stray voltage/current than normal, then the galvanic isolator will not be able to able to protect you. Also, there have been cases of the diodes failing in galvanic isolators and this can then leave your vessel with no earth connection. For this reason it is good practice to test your galvanic isolator regularly, using the following procedure.
Testing a Galvanic Isolator
1. Make sure you are disconnected from the AC shore supply
2. Set your multimeter to the Diode Test setting
3. Locate the Galvanic Isolator and its two earth connections
4. Connect one lead to the Shore Earth and the other lead to the Boat’s Earth connection
5. Make sure the multimeter shows a voltage between 0.6v and 1.4v
6. Swap the leads over and you should again read a voltage between 0.6v and 1.4v
7. On my Victron VDI-32, I measured approximately 0.85v in both directions
You can also use the multimeter (set to DC voltage) to check what level of stray current/voltage is being blocked, just connect the two test leads to the two earth connections again and you should read a smaller voltage – hopefully less than the voltage measured in the diode test. In my test it was 139mV (0.139v) which is well below the 0.86v diode voltage and therefore is being blocked. If you measure a DC voltage greater than the diode test voltage, then you have a serious level of stray current and need to investigate further with the marina.
If you have the space and budget for an Isolation Transformer, then this provides total AC isolation. We decided to go the galvanic isolator route, but if we were continuously connected to an AC shore supply, we probably would have gone for an isolation transformer.
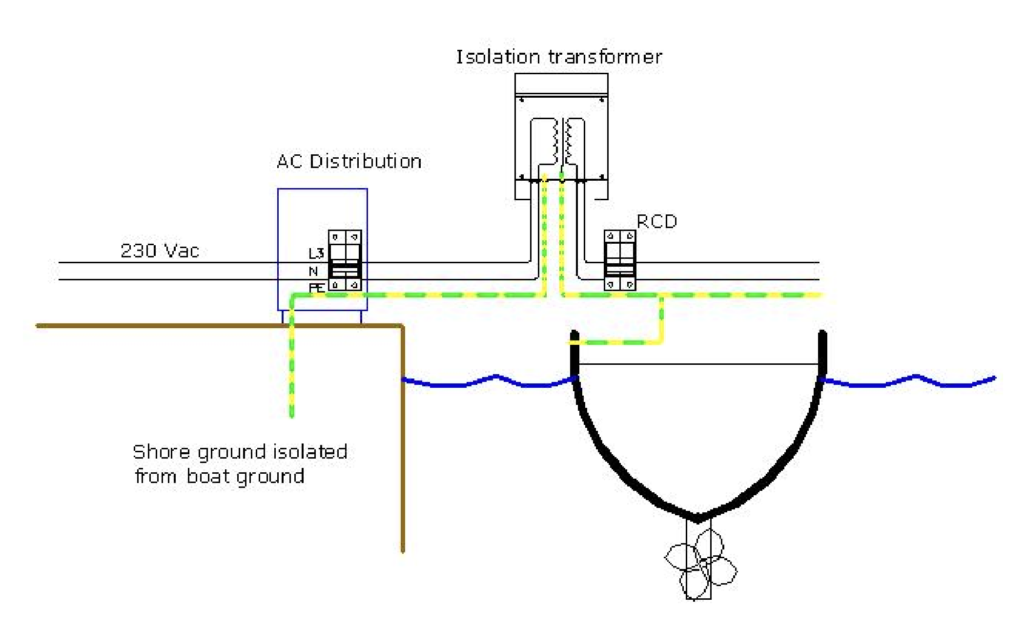
It will be interesting to see whether there are any signs of galvanic corrosion, when “Old Nick” comes out of the water next month, but we hope that our Victron VDI-32 has been doing its job and our hull just needs blacking and nothing more.
If you would like some further reading on this subject, I would recommend this article…
https://www.victronenergy.com/blog/2016/01/11/boat-electrical-installations-combating-seawater/
Oops! Good spot. You can tell that my background in Marine electronics is from the salty sector of the market! THank you.
Hi Paul,
interesting article, but Magnesium anodes are more commonly used in fresh water, with zinc used with sea water. aluminium can apparantly be used for either, although I never came across any myself.
Rgds
Pete